Astratto
La stabilità della temperatura è fondamentale per le prestazioni dell'ultravioletto completamente allo stato solido (UV) Laser viola a picosecondi, influenzandone le caratteristiche di output e l’efficienza. Questo articolo presenta un innovativo sistema di controllo della temperatura che impiega un sistema di refrigerazione DC inverter del tipo a compressione di vapore accoppiato con compensazione elettrotermica. Il sistema sfrutta la derivazione proporzionale-integrale (PID) controllo per regolare la velocità e la potenza elettrica di un compressore micro DC inverter, consentendo una regolazione precisa ed efficiente della temperatura. I risultati sperimentali dimostrano che il sistema raggiunge una rapida stabilizzazione (6 minuti) e alta precisione (±0,01°C), rendendolo una soluzione economica e compatta per le crescenti applicazioni dei laser UV nella marcatura, taglio di precisione, e altre industrie.
1. L'evoluzione dei laser UV completamente allo stato solido
Laser UV, con lunghezze d'onda ≤400 nm, sono indispensabili in settori come il monitoraggio ambientale, medicinale, e microfabbricazione a causa della loro corta lunghezza d'onda, alta risoluzione, ed energia concentrata. Lo sviluppo di laser UV interamente a stato solido, che utilizzano diodi laser (LD) come pompe, ha rivoluzionato questo campo superando i limiti dei laser a gas e ad eccimeri, come quelle di grandi dimensioni, bassa efficienza, e costo elevato. Le innovazioni degli anni '90 e i successivi progressi hanno consolidato l'importanza dei laser UV interamente a stato solido per diverse applicazioni, compresa la lavorazione di materiali di precisione e trattamenti medici.
2. Sfide nel controllo della temperatura dei laser UV interamente a stato solido
Le prestazioni dei laser UV interamente a stato solido sono altamente sensibili alle variazioni di temperatura, influenzando la stabilità LD e l'efficienza del cristallo ottico non lineare. Il calore generato durante il pompaggio LD e la conversione di frequenza deve essere dissipato in modo efficace per prevenire variazioni dell'indice di rifrazione e deriva della lunghezza d'onda, che degradano l'emissione del laser. Metodi di raffreddamento tradizionali come sistemi basati su ventola o raffreddamento termoelettrico (TECNICO) affrontare limitazioni in termini di efficienza, stabilità, e scalabilità. Una soluzione più efficace risiede nei sistemi avanzati raffreddati ad acqua che utilizzano compressori CC miniaturizzati.
3. Principi del sistema di controllo della temperatura
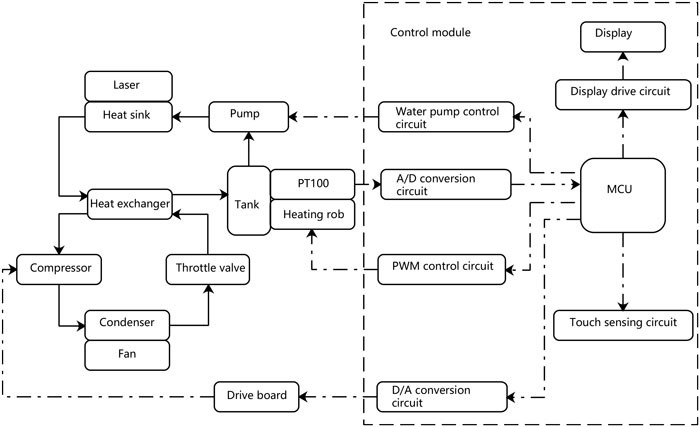
Panoramica del sistema:
Il sistema proposto integra un circuito di raffreddamento ad acqua e un ciclo di refrigerazione a compressione di vapore. I componenti chiave includono:
- Scambiatore di calore: Facilita il trasferimento di calore tra acqua e refrigerante.
- Compressore: Un compressore DC inverter in miniatura (Ecco alcuni dettagli sui modelli di mini compressori di Coolingstyle) regola dinamicamente la capacità di raffreddamento.
- Riscaldatore elettrico: Fornisce la regolazione fine e compensa il superamento del raffreddamento.
- Sensore di temperatura: Un sensore Pt100 garantisce un monitoraggio della temperatura ad alta precisione.
Operazione:
L'acqua assorbe il calore dal laser e circola attraverso lo scambiatore di calore, dove il refrigerante lo raffredda. Il controllo PID regola la velocità del compressore e la potenza del riscaldatore per stabilizzare la temperatura dell'acqua, garantendo un funzionamento laser coerente.
4. Hardware e funzionalità del sistema
4.1 Sistema di refrigerazione
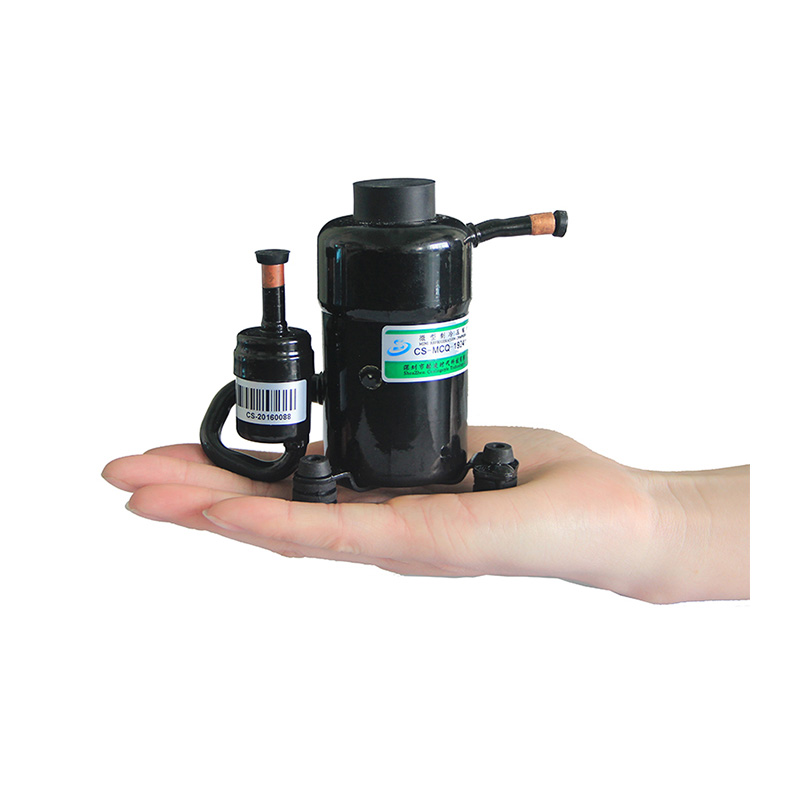
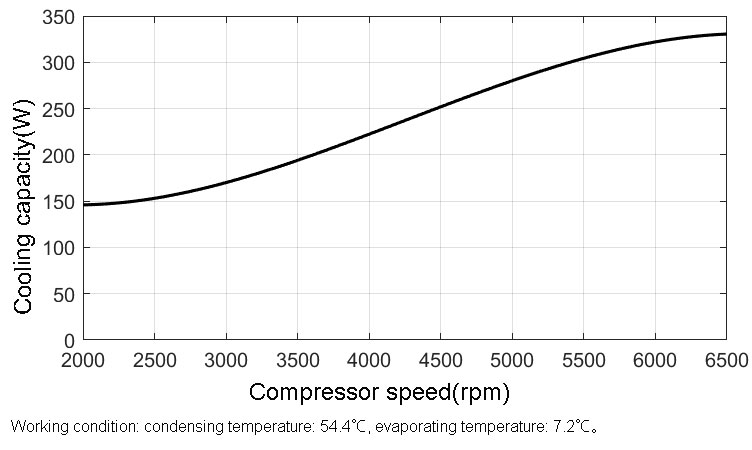
Il compressore DC inverter compatto (56 diametro mm, 850 peso g) raggiunge velocità variabili per modulare la capacità di raffreddamento. La sua curva di prestazione (Figura 3) evidenzia la sua adattabilità, rendendolo ideale per un controllo preciso della temperatura.
4.2 Unità di riscaldamento
Un riscaldatore elettrico compensa le fluttuazioni di temperatura e previene il raffreddamento eccessivo in condizioni di basso carico. Utilizzando il controllo PWM, il riscaldatore fornisce regolazioni precise della potenza.
4.3 Rilevamento della temperatura
Un sensore Pt100 con configurazione a tre fili garantisce letture accurate della temperatura eliminando gli effetti della resistenza del filo. I dati del sensore, elaborato tramite un convertitore A/D, informa l'algoritmo di controllo PID.
4.4 Controllo PID
L'algoritmo PID regola dinamicamente la velocità del compressore e la potenza del riscaldatore in base agli errori di temperatura in tempo reale. Questo processo iterativo riduce al minimo il tempo di stabilizzazione e mantiene la precisione di ±0,01°C.
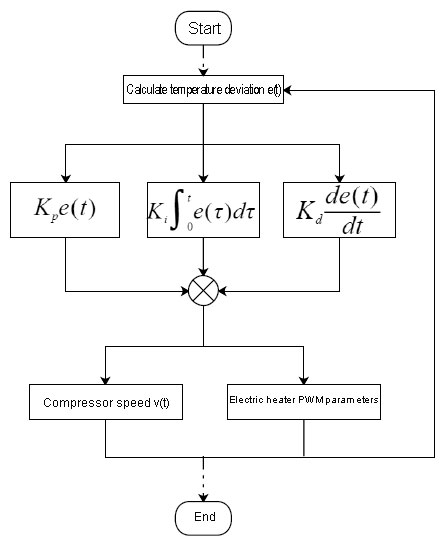
5. Validazione sperimentale
Prova di configurazione:
Sono stati utilizzati un laser UV da 10 W e un circuito di raffreddamento ad acqua da 1 litro. La temperatura target è stata fissata a 25°C. Figura 6 mostra il processo di stabilizzazione della temperatura.
Risultati:
- Tempo di stabilizzazione: 6 minuti.
- Precisione della temperatura: ±0,01°C.
Il sistema ha mantenuto efficacemente la temperatura operativa del laser, confermando la sua elevata precisione e reattività.
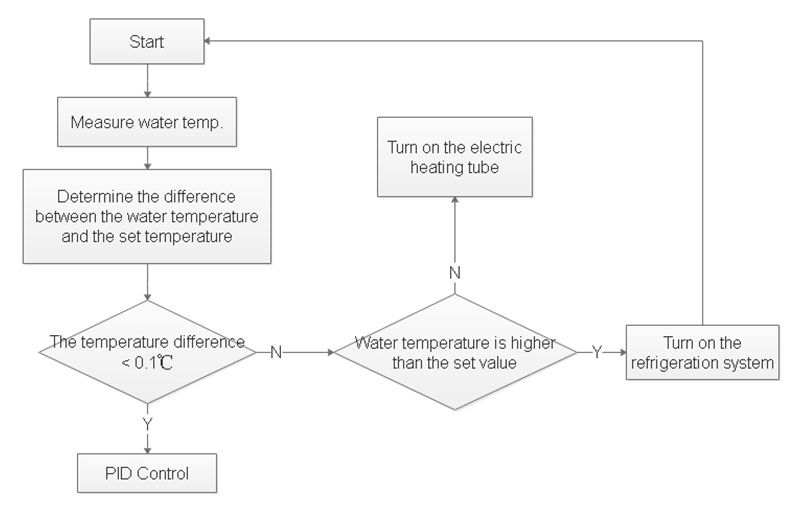
6. Vantaggi comparativi
Rispetto ai metodi di raffreddamento tradizionali:
- Dimensioni compatte & Peso leggero: Ideale per applicazioni con vincoli di spazio.
- Efficienza energetica: Capacità di raffreddamento superiore e consumo energetico ridotto.
- Efficacia in termini di costi: Competitivo con i sistemi TEC offrendo allo stesso tempo una maggiore precisione.
- Versatilità: Compatibilità con vari standard di alimentazione.
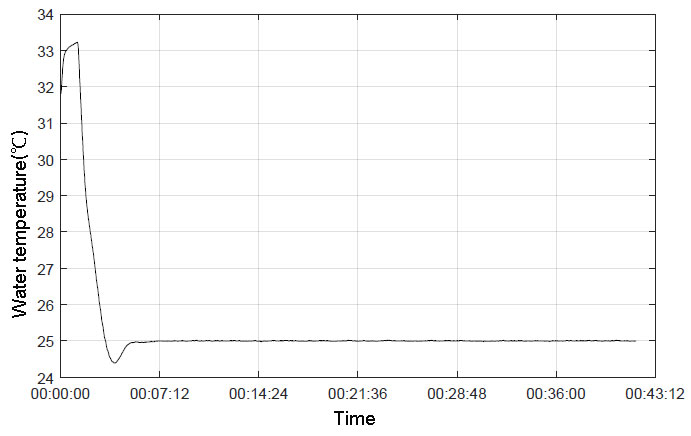
7. Conclusione
Questo studio introduce un sistema di controllo della temperatura ad alta precisione per laser UV interamente a stato solido, sfruttando un compressore CC miniaturizzato e una compensazione elettrotermica. Il design compatto del sistema, rapida stabilizzazione, e precisione eccezionale (±0,01°C) lo rendono una soluzione pratica per applicazioni industriali come la marcatura e il taglio di precisione. La sua scalabilità ed efficienza rappresentano una promessa significativa per il progresso delle tecnologie di raffreddamento laser e la promozione della loro adozione diffusa.
Bibliografia
[1] Maiman T H. Radiazione ottica stimolata nel rubino [J]. Natura, 1960, 187.
[2] Fu, Zhehong. Applicazione e sviluppo del laser [J]. Tecnologia elettronica e ingegneria del software, 2017(5).
[3] Shen Zhaoguo. Ricerca sui laser verdi e ultravioletti da 355 nm pompati con LD [D]. Università nordoccidentale, 2009.
[4] Ok M, Liu L Y. Tutti i Nd a stato solido ad onda continua quadruplicati in frequenza: Laser YAG [J]. Rivista IEEE di argomenti selezionati nell'elettronica quantistica, 1995, 1(3):P.859-866.
[5] N. Hodgson, D. Dudley, l. Gruber, et al. Pompaggio a diodi, TEM/sub 00/ ND: YVO/sott 4/ laser con potenza di uscita maggiore di 12 W a 355 nm[C]// Convegno sui Laser & Elettroottica. IEEE, 2001.
[6] David R. Dudley, Oliver Mehl, Gary Y. Wang, et al. Nd. pompato a diodi Q-switched: Laser a barra YAG con potenza di uscita di 420 W a 532 nm e 160 W a 355 nm [J]. Atti della Spie, la Società Internazionale di Ingegneria Ottica, 2009, 7193(1):28.
[7] Chen G.F., Wang X.H., Tu Gogo. Ricerca su tutti i laser ultravioletti a stato solido [J]. Giornale di fotonica, 1999(09):785-788.
[8] Shaolin Wang, Kaifa Cao, Zong Ming Tao, et al. Ricerca sul sistema spettroscopico del vapore acqueo ultravioletto Raman Lidar [J]. Giornale di optoelettronica-laser, 2010, 21 (08):1171-1175.
[9] Xue Chun Tan. Dispositivo di simulazione radar laser e ricerca sperimentale [D]. Università della Scienza e della Tecnologia di Changchun, 2012
[10] McGill Matteo, Capo Dennis, Hart William, et al. Lidar per la fisica delle nuvole: descrizione dello strumento e risultati iniziali delle misurazioni. 2002, 41(18):3725-34.
[11] Yang Wang, Xu bao Wang, Zhanling Dong, et al. Espressione della proteina γ del recettore attivato dalla proliferazione del perossisoma e della β-catenina nei tessuti epatici irradiati mediante laser ultravioletto[J]. Giornale cinese di ricerca sull'ingegneria dei tessuti, 2011,15(33):6191-6195.
[12] Luglio It, Keni Qiu. L'applicazione della comunicazione ultravioletta nel sistema di comunicazione militare. Ottica & Tecnologia optoelettronica[J],2005( 04):19-21.
[13] No S. l., Guan Y. C. Laser ultravioletti e sua applicazione nella microlavorazione [J]. Ingegneria optoelettronica, 2017, 44(12):1169-1179+1251.
[14] Wang D. Esplorazione della generazione e delle applicazioni di laser a femtosecondi UV profondi e UV sotto vuoto [D]. Università Normale della Cina Orientale, 2016.
[15] T.G. Kim, Io Ogura. Temperatura caratteristica elevata (T o=322 K vicino alla temperatura ambiente) di laser a diodi a filo quantico Al GaAs-GaAs con scanalatura a V[J]. Elettronica a stato solido, 2000, 44(1).
[16] Quella L, Ling è, Nave, Tian F, Bai JT. Ricerca sul campo di temperatura del cristallo non lineare KTP nel sistema laser raffreddato ad acqua[J]. Laser & Infrarossi, 2005(01):51-54.
[17] Zeng H-L, Jiang PF, Xie F-Zeng. Ricerca sul controllo della temperatura dei laser a semiconduttore [J]. Laser e Infrarossi, 2004(05):339-340+346.
1 Un commentoControllo preciso della temperatura per laser UV completamente a stato solido utilizzando sistemi di compressione CC miniaturizzati: Un approccio innovativo”
This is my first time pay a visit at here and i am truly happy to read all at single place.