Lasers, first invented in the 1960s, have become indispensable tools across various industries. However, as with all high-energy devices, managing the heat they generate is critical to ensuring their performance, lifespan, and safety. Let’s explore what lasers are, their applications, and how to manage their thermal needs effectively.
What is a Laser?
A laser is a device that emits light through optical amplification, with its name standing for Light Amplification by Stimulated Emission of Radiation. Lasers are known for their precision, power, and versatility.
Applications of Lasers:
- Consumer Industry:
- Since 1974, laser scanners have been used to read barcodes in retail settings.
- Manufacturing:
- Lasers are essential for engraving, cutting, drilling, and marking various materials.
- Medical Field:
- Used in surgeries, laser eye treatments, and cosmetic procedures.
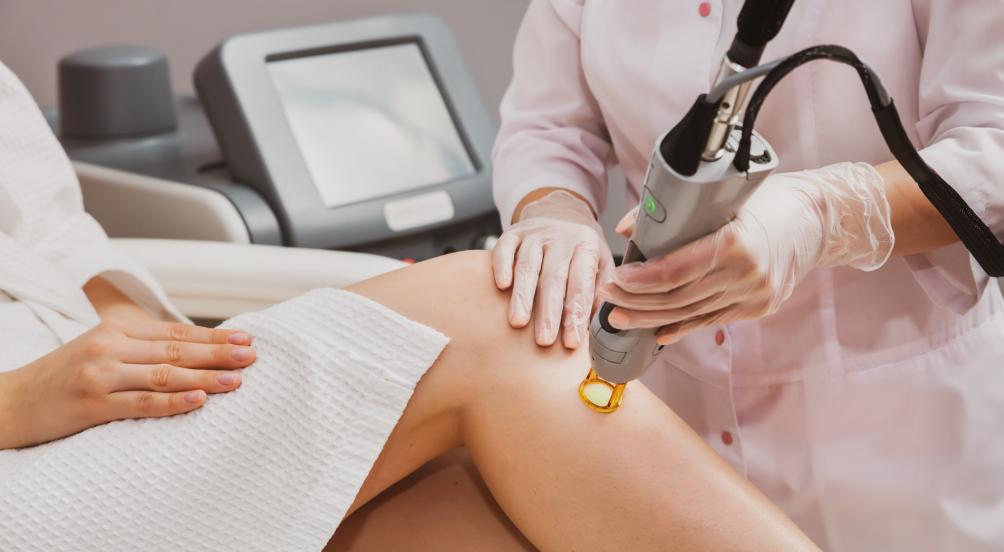
4. Military:
- High-energy lasers are employed for applications such as destroying unmanned aerial vehicles.
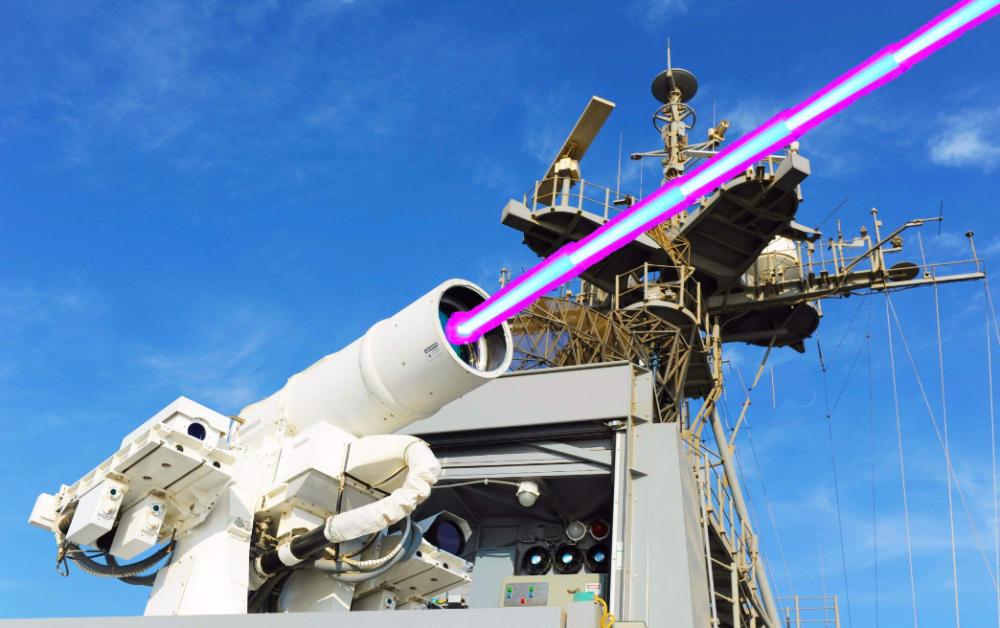
Why Do Lasers Need Thermal Management?
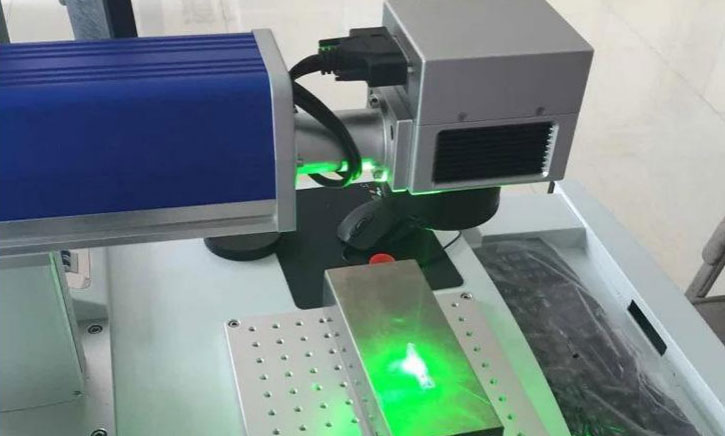
During operation, only a fraction of the electrical energy in a laser is converted into laser energy. A significant portion is lost as heat. Proper thermal management is essential to:
- Maintain Functionality:
- Prevent overheating, which can degrade performance or damage the laser components.
- Enhance Longevity:
- Prolong the lifespan of the laser by mitigating thermal stress.
- Ensure Precision:
- Temperature fluctuations can alter the frequency of the laser light, reducing output quality.
Choosing the Right Chiller for Your Laser
Selecting an appropriate chiller is critical for effective laser cooling. Here are the key considerations:
1. Cooling Capacity
- Heat Load: This is the minimum capacity a chiller must have to cool the laser, typically measured in watts or BTU/hr.
- Nominal Cooling Capacity: Usually specified at 25℃ coolant output and ambient air temperature.
- Tip: If the heat load isn’t known, use the laser’s power consumption as a reference to select a chiller with sufficient cooling capacity.
2. Coolant Selection
- Types of Coolants:
- Distilled or Tap Water: Commonly treated with algaecides or glycol additives.
- Deionized Water: For lasers that require ultra-pure coolant, ensure compatibility with DI materials.
- Water-Glycol Mixture: Ideal for low-temperature environments to prevent freezing.
3. Pump Performance
- Flow Rate and Pressure:
- Choose a pump that provides a steady flow rate.
- Avoid excessively high pressure to prevent pipe damage or leakage, and low pressure that might hinder coolant circulation.
4. Additional Features
- Communication Interfaces: RS-485 or similar allows for remote monitoring and control of chiller parameters like temperature and flow rate.
- Alarms: High/low-temperature and low-flow alarms safeguard the laser and chiller.
- Filters: Protect the laser and pump from particles in the coolant.
Advantages of Using Industrial Chillers
- Enhanced Performance: Maintain stable operating conditions for consistent laser output.
- Increased Lifespan: Protect laser components from thermal damage.
- Versatility: Support a wide range of lasers and operational environments.
- Energy Efficiency: Modern chillers offer optimized cooling with minimal energy consumption.
Understanding Lasers and Their Thermal Management Needs
Lasers, first invented in the 1960s, have become indispensable tools across various industries. However, as with all high-energy devices, managing the heat they generate is critical to ensuring their performance, lifespan, and safety. Let’s explore what lasers are, their applications, and how to manage their thermal needs effectively.
What is a Laser?
A laser is a device that emits light through optical amplification, with its name standing for Light Amplification by Stimulated Emission of Radiation. Lasers are known for their precision, power, and versatility.
Applications of Lasers:
- Consumer Industry:
- Since 1974, laser scanners have been used to read barcodes in retail settings.
- Manufacturing:
- Lasers are essential for engraving, cutting, drilling, and marking various materials.
- Medical Field:
- Used in surgeries, laser eye treatments, and cosmetic procedures.
- Military:
- High-energy lasers are employed for applications such as destroying unmanned aerial vehicles.
Why Do Lasers Need Thermal Management?
During operation, only a fraction of the electrical energy in a laser is converted into laser energy. A significant portion is lost as heat. Proper thermal management is essential to:
- Maintain Functionality:
- Prevent overheating, which can degrade performance or damage the laser components.
- Enhance Longevity:
- Prolong the lifespan of the laser by mitigating thermal stress.
- Ensure Precision:
- Temperature fluctuations can alter the frequency of the laser light, reducing output quality.
How to Manage Laser Thermal Needs?
Lasers, especially high-energy types like CO₂, disk, diode, and fiber lasers, require robust cooling systems. Industrial chillers are the most commonly used solution for laser cooling.
Industrial Chillers:
Chillers provide a stable temperature by circulating coolant through the laser’s resonators, optics, and heads, even under load fluctuations. High precision in temperature control enhances laser performance.
Choosing the Right Chiller for Your Laser
Selecting an appropriate chiller is critical for effective laser cooling. Here are the key considerations:
1. Cooling Capacity
- Heat Load: This is the minimum capacity a chiller must have to cool the laser, typically measured in watts or BTU/hr.
- Nominal Cooling Capacity: Usually specified at 25℃ coolant output and ambient air temperature.
- Tip: If the heat load isn’t known, use the laser’s power consumption as a reference to select a chiller with sufficient cooling capacity.
2. Coolant Selection
- Types of Coolants:
- Distilled or Tap Water: Commonly treated with algaecides or glycol additives.
- Deionized Water: For lasers that require ultra-pure coolant, ensure compatibility with DI materials.
- Water-Glycol Mixture: Ideal for low-temperature environments to prevent freezing.
3. Pump Performance
- Flow Rate and Pressure:
- Choose a pump that provides a steady flow rate.
- Avoid excessively high pressure to prevent pipe damage or leakage, and low pressure that might hinder coolant circulation.
4. Additional Features
- Communication Interfaces: RS-485 or similar allows for remote monitoring and control of chiller parameters like temperature and flow rate.
- Alarms: High/low-temperature and low-flow alarms safeguard the laser and chiller.
- Filters: Protect the laser and pump from particles in the coolant.
Advantages of Using Industrial Chillers
- Enhanced Performance: Maintain stable operating conditions for consistent laser output.
- Increased Lifespan: Protect laser components from thermal damage.
- Versatility: Support a wide range of lasers and operational environments.
- Energy Efficiency: Modern chillers offer optimized cooling with minimal energy consumption.
Conclusion
Efficient thermal management is vital for any laser system, ensuring both its functionality and durability. By carefully selecting a chiller with appropriate cooling capacity, reliable coolant, and advanced features, you can maintain your laser at peak performance. With the right solution, lasers can continue to excel in their diverse applications across industries.