Abstract
Temperature stability is crucial for the performance of all-solid-state ultraviolet (UV) lasers, influencing their output characteristics and efficiency. This paper presents an innovative temperature control system employing a vapor compression type DC inverter refrigeration system coupled with electrothermal compensation. The system leverages Proportional-Integral-Derivative (PID) control to adjust the speed and electric power of a micro DC inverter compressor, enabling precise and efficient temperature regulation. Experimental results demonstrate that the system achieves rapid stabilization (6 minutes) and high accuracy (±0.01°C), making it a cost-effective and compact solution for the growing applications of UV lasers in marking, precision cutting, and other industries.
1. The Evolution of All-Solid-State UV Lasers
UV lasers, with wavelengths ≤400 nm, are indispensable in industries like environmental monitoring, medicine, and microfabrication due to their short wavelength, high resolution, and concentrated energy. The development of all-solid-state UV lasers, which use laser diodes (LDs) as pumps, has revolutionized this field by overcoming the limitations of gas and excimer lasers, such as large size, low efficiency, and high cost. Innovations in the 1990s and subsequent advancements have solidified the importance of all-solid-state UV lasers for diverse applications, including precision material processing and medical treatments.
2. Challenges in Temperature Control of All-Solid-State UV Lasers
The performance of all-solid-state UV lasers is highly sensitive to temperature variations, affecting LD stability and nonlinear optical crystal efficiency. Heat generated during LD pumping and frequency conversion must be effectively dissipated to prevent refractive index changes and wavelength drift, which degrade laser output. Traditional cooling methods like fan-based systems or thermoelectric cooling (TEC) face limitations in efficiency, stability, and scalability. A more effective solution lies in advanced water-cooled systems employing miniature DC compressors.
3. Principles of the Temperature Control System
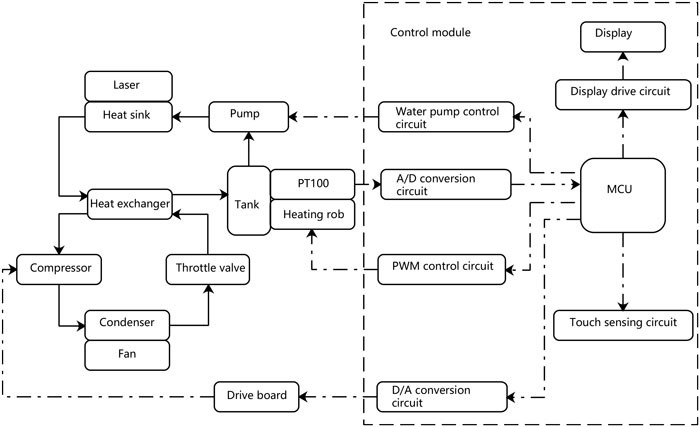
System Overview:
The proposed system integrates a water-cooling loop and a vapor compression refrigeration cycle. Key components include:
- Heat Exchanger: Facilitates heat transfer between water and refrigerant.
- Compressor: A miniature DC inverter compressor (CS-MCQ-19241100) dynamically adjusts cooling capacity.
- Electric Heater: Provides fine-tuning and compensates for cooling overshoot.
- Temperature Sensor: A Pt100 sensor ensures high-precision temperature monitoring.
Operation:
Water absorbs heat from the laser and circulates through the heat exchanger, where refrigerant cools it. PID control adjusts compressor speed and heater power to stabilize the water temperature, ensuring consistent laser operation.
4. System Hardware and Functionality
4.1 Refrigeration System
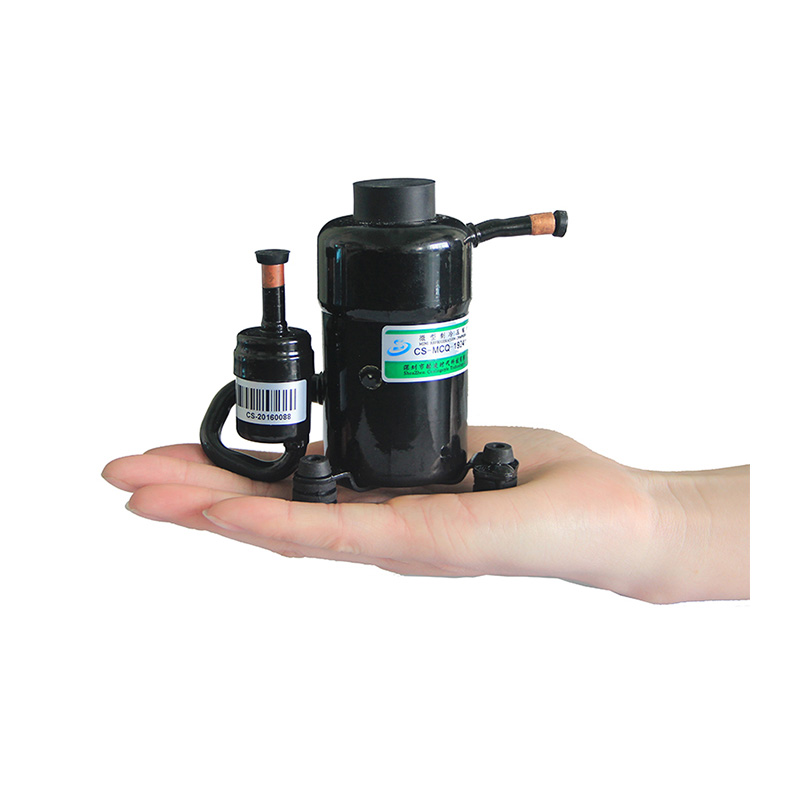
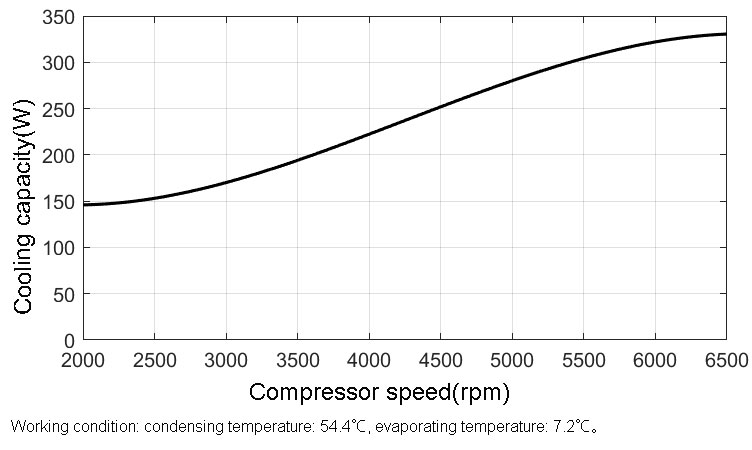
The compact DC inverter compressor (56 mm diameter, 850 g weight) achieves variable speeds to modulate cooling capacity. Its performance curve (Figure 3) highlights its adaptability, making it ideal for precise temperature control.
4.2 Heating Unit
An electric heater compensates for temperature fluctuations and prevents overcooling during low-load conditions. Using PWM control, the heater provides precise power adjustments.
4.3 Temperature Sensing
A Pt100 sensor with a three-wire configuration ensures accurate temperature readings by eliminating wire resistance effects. The sensor’s data, processed through an A/D converter, informs the PID control algorithm.
4.4 PID Control
The PID algorithm dynamically adjusts compressor speed and heater power based on real-time temperature errors. This iterative process minimizes stabilization time and maintains ±0.01°C accuracy.
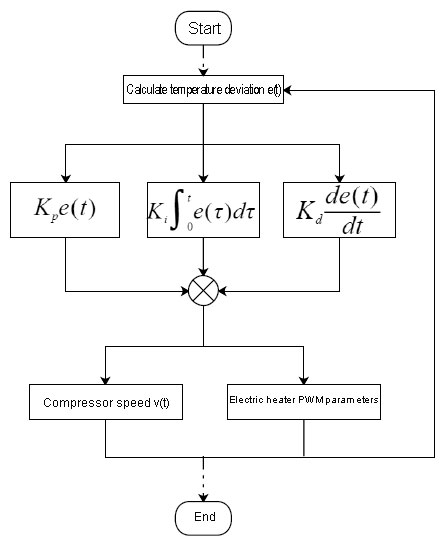
5. Experimental Validation
Test Setup:
A 10W UV laser and a 1L water cooling loop were used. The target temperature was set at 25°C. Figure 6 shows the temperature stabilization process.
Results:
- Stabilization Time: 6 minutes.
- Temperature Accuracy: ±0.01°C.
The system effectively maintained laser operating temperature, confirming its high precision and responsiveness.
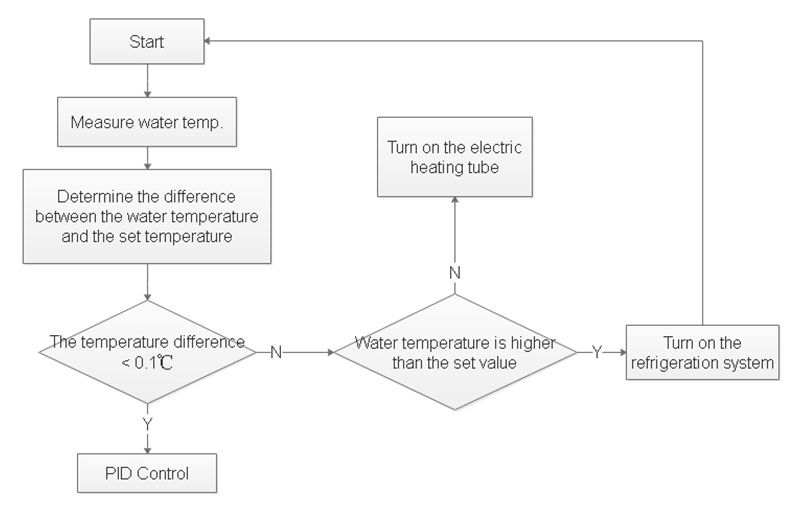
6. Comparative Advantages
Compared to traditional cooling methods:
- Compact Size & Light Weight: Ideal for space-constrained applications.
- Energy Efficiency: Superior cooling capacity and reduced energy consumption.
- Cost-Effectiveness: Competitive with TEC systems while offering higher accuracy.
- Versatility: Compatibility with various power supply standards.
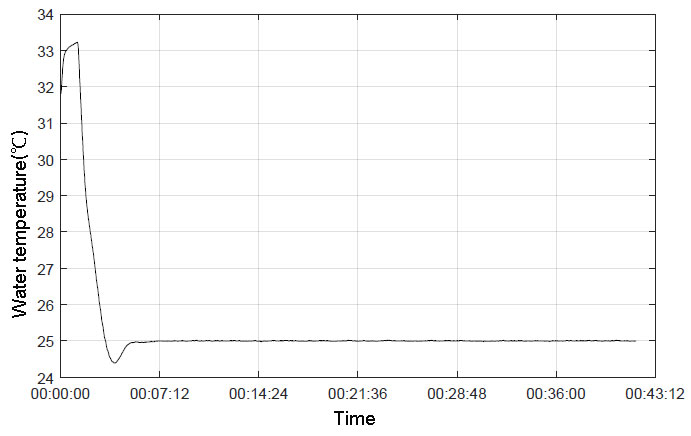
7. Conclusion
This study introduces a high-precision temperature control system for all-solid-state UV lasers, leveraging a miniature DC compressor and electrothermal compensation. The system’s compact design, rapid stabilization, and exceptional accuracy (±0.01°C) make it a practical solution for industrial applications like marking and precision cutting. Its scalability and efficiency hold significant promise for advancing laser cooling technologies and promoting their widespread adoption.
Bibliography
[1] Maiman T H. Stimulated optical radiation in ruby [J]. Nature, 1960, 187.
[2] Fu, Zhehong. Application and development of laser [J]. Electronic Technology and Software Engineering, 2017(5).
[3] Shen Zhaoguo. Research on LD-Pumped 532nm Green and 355nm Ultraviolet Lasers [D]. Northwestern University, 2009.
[4] Oka M, Liu L Y. All solid-state continuous-wave frequency-quadrupled Nd: YAG laser [J]. IEEE journal of selected topics in quantum electronics, 1995, 1(3):P.859-866.
[5] N. Hodgson, D. Dudley, L. Gruber, et al. Diode end-pumped, TEM/sub 00/ Nd: YVO/sub 4/ laser with output power greater than 12 W at 355 nm[C]// Conference on Lasers & Electro-optics. IEEE, 2001.
[6] David R. Dudley, Oliver Mehl, Gary Y. Wang, et al. Q-switched diode-pumped Nd: YAG rod laser with output power of 420W at 532nm and 160W at 355nm [J]. Proceedings of Spie the International Society for Optical Engineering, 2009, 7193(1):28.
[7] Chen G.F., Wang X.H., Du Gogo. Research on All Solid-State Ultraviolet Lasers [J]. Journal of Photonics, 1999(09):785-788.
[8] Shaolin Wang, Kaifa Cao, Zong Ming Tao, et al. Research on Spectroscopic System of Water Vapor Ultraviolet Raman Lidar [J]. Journal of Optoelectronics-Laser, 2010, 21 (08):1171-1175.
[9] Xue chun Tan. Laser Radar Simulation Device and Experimental Research [D]. Changchun University of Science and Technology, 2012
[10] McGill Matthew, Hlavka Dennis, Hart William, et al. Cloud physics lidar: instrument description and initial measurement results. 2002, 41(18):3725-34.
[11] Yang Wang, Xu bao Wang, Zhan ling Dong, et al. Expression of β-Catenin and Peroxisome Proliferator-Activated Receptor γ Protein in Liver Tissues Irradiated by Ultraviolet Laser[J]. Chinese Journal of Tissue Engineering Research, 2011,15(33):6191-6195.
[12] Jiye Li, Keni Qiu. The Application of Ultraviolet Communication in Military Communication System. Optics & Optoelectronic Technology[J],2005( 04):19-21.
[13] Nie S. L., Guan Y. C. Ultraviolet Lasers and Its Application in Micro-machining [J]. Optoelectronic Engineering, 2017, 44(12):1169-1179+1251.
[14] Wang D. Exploration of deep UV and vacuum UV femtosecond laser generation and applications [D]. East China Normal University, 2016.
[15] T.G Kim, M Ogura. High characteristic temperature (T o=322 K near room temperature) of V-grooved Al GaAs-GaAs quantum wire diode lasers[J]. Solid State Electronics, 2000, 44(1).
[16] Li L, Ling YW, Shi P, Tian F, Bai JT. Research on Temperature Field of Nonlinear Crystal KTP in Water-Cooled Laser System[J]. Laser & Infrared, 2005(01):51-54.
[17] Zeng H-L, Jiang P-F, Xie F-Zeng. Research on temperature control of semiconductor lasers [J]. Laser and Infrared, 2004(05):339-340+346.
1 thought on “Precise Temperature Control for All-Solid-State UV Lasers Using Miniature DC Compressor Systems: A Novel Approach”
This is my first time pay a visit at here and i am truly happy to read all at single place.